WORKSHOPS
Our workshops empower individuals and teams to gain relevant, actionable skills and knowledge that can be applied immediately. Using hands-on exercises, engaging discussions, and relevant examples, we foster a deeper learning experience.
In partnership with MoreSteam, we incorporate computer-based simulations to allow participants to apply their learnings and practice their skills immediately. We instill confidence and equip participants with new tools they can put to work the right way.
We Offer The Following Workshops:
Empower Leaders
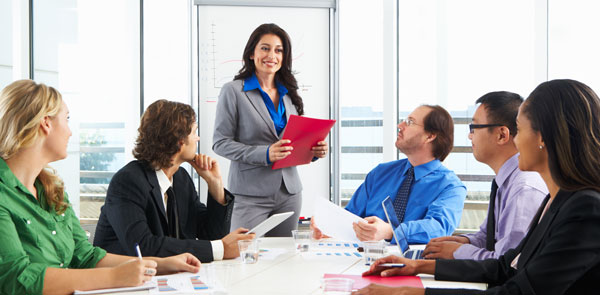
Performance-minded Leader
Coaching for Performance
Empower Teams
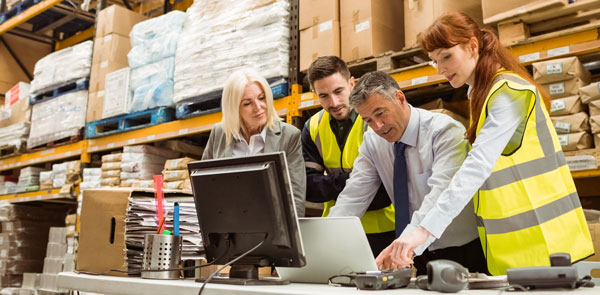
Lean Essentials
Leading Kaizen Events
Lean Six Sigma Yellow Belt
Team Leadership
Empower Growth
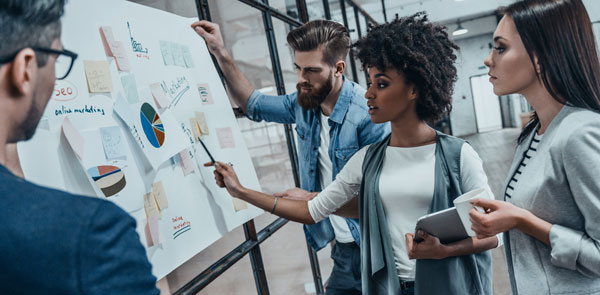
Lean Essentials
Lean Six Sigma Yellow Belt
Improve Daily Work
Empower Leaders
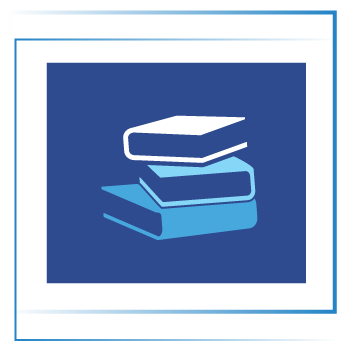
Performance-minded Leader —2 Days
Purpose
To equip senior leaders with an overview of Lean Six Sigma methods and tools, how to link process improvement activities with strategic objectives, and how to effectively select process improvement projects and practitioners. This workshop includes a hands-on process simulation to enhance the learning experience.
Target Audience
Senior leaders who will promote and oversee process improvement in their organizations.
Learning Objectives
- Understand the purpose, focus, and benefits of Lean Six Sigma as an improvement methodology
- Link process improvement activities to strategic planning and achieving strategic objectives
- Identify the governance and infrastructure elements required to establish a successful Lean Six Sigma program
- Understand the Define-Measure-Analyze-Improve-Control (DMAIC) improvement models to guide process improvement actions
- Utilize standard criteria to effectively select process improvement projects and practitioners
- Learn transformational leadership behaviors to promote successful process improvement
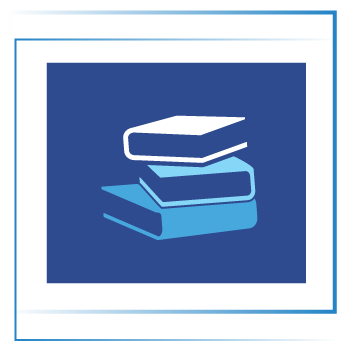
Coaching for Performance —1 Day
Purpose
To equip participants with knowledge of the basic coaching process, active listening and effective questioning skills, and behaviors that will enhance their ability to formally or informally coach others within their organization.
Target Audience
Any leader, department manager, supervisor or individual contributor seeking to function as a coach to others in the organization and increase their coaching effectiveness.
Learning Objectives
- Define what coaching is/is not
- Identify key coaching competencies
- Understand how coaching aligns with your role as a leader
- Utilize the GROW coaching model
- Employ active listening and effective questioning techniques
- Apply coaching best practices throughout the DMAIC cycle (optional)
- Strengthen skills to engage, motivate and drive performance
Empower TEAMS
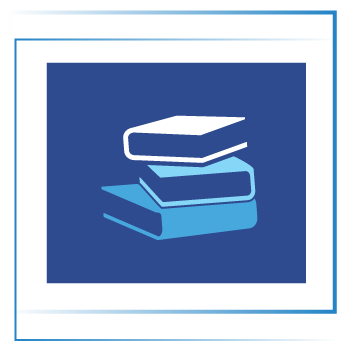
Lean Essentials —5 Days
Purpose
To develop participants as internal experts to successfully lead and execute Lean improvement activities within their organization.
Target Audience
Individuals at any level who will lead and execute Lean improvement efforts to improve the efficiency of operations within their organization.
Learning Objectives
- Understand the purpose, objectives, results, and benefits of applying Lean within their organization
- Recognize the five core principles of Lean
- Assess areas of waste within the organization and identify the two key drivers of waste
- Identify, document, and assess Value Streams for improvement opportunities
- Implement Lean tools and methods to tackle waste
- Utilize the A3 framework for problem solving
- Execute Lean improvement efforts using Kaizen/Rapid Improvement Event
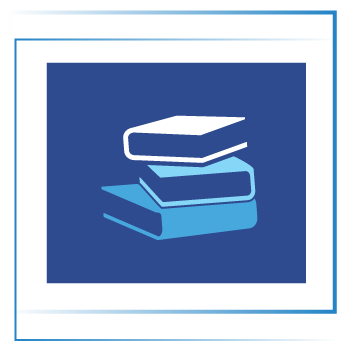
Leading Kaizen Events —4 Days
Purpose
To develop participants as internal experts to successfully plan and lead Lean (Kaizen) events within their organization. This workshop includes an interactive simulation for participants to apply their learnings immediately.
Target Audience
Individuals at any level who will lead teams through Lean (Kaizen) rapid improvement efforts to improve operations within their organization. Participants should have a basic knowledge of Lean concepts (such as Lean Fundamentals).
Learning Objectives
- Understand the purpose, objectives, and benefits of executing Lean (Kaizen) events
- Utilize the A3 framework for problem-solving
- Recognize the three phases of Lean (Kaizen) events – Plan, Conduct, and Follow-up
- Conduct pre-event planning activities such as identifying opportunities, team formation, project chartering, and project planning.
- Execute Lean (Kaizen) events to understand the current state, conduct root cause analysis, and implement Lean improvements to tackle waste.
Tools May Include (can be customized for your needs):- Types of waste
- Takt time
- Measuring cycle time
- 5S
- Error-proofing
- Standard work
- Single Minute Exchange of Dies (SMED)
- One-piece flow and pull
- Kanban
- Production/load leveling
- Conduct follow-up activities such as control planning, A3 storytelling, and project closeout. Tools include (can be customized for your needs):
- Control plan
- Visual management and controls
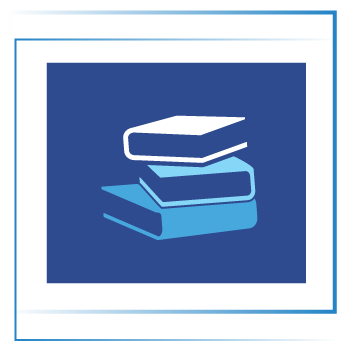
Lean Six Sigma Yellow Belt —3 Days
Purpose
To equip participants with a working knowledge of the Lean Six Sigma improvement methodology, key concepts, and tools used.
Target Audience
Individuals at any level of the organization (front line, supervisor, manager, etc.) who will either participate on a Lean Six Sigma project team or who will work on small-scale improvement efforts within their own areas.
Learning Objectives
- Understand the purpose and focus of Lean Six Sigma as an improvement methodology
- Communicate with a common language of key Lean Six Sigma terms
- Identify activities in the organization as processes
- Define suppliers, inputs, process steps, outputs, and customers of processes
- Understand and apply the Define-Measure-Analyze-Improve-Control (DMAIC) improvement models to guide process improvement actions
- Apply key DMAIC tools such as project charter, process mapping, basic data analysis techniques, Sigma capability, and root cause analysis
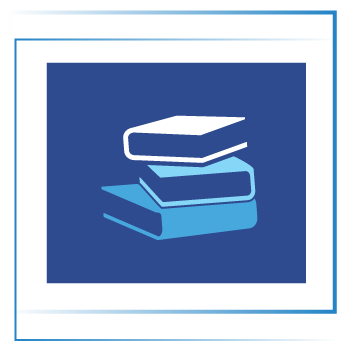
Team Leadership—2 Days
Purpose
To provide participants with knowledge, skills and techniques to successfully facilitate teams and serve as team leaders within their organization.
Target Audience
Individuals who work in, and lead teams.
Learning Objectives
- Identify what makes a team, types of teams, and team roles
- Understand and recognize the stages of team performance, and how to facilitate teams through the stages
- Utilize and lead others in effective speaking and listening skills
- Apply a variety of techniques for guiding discussions
- Address conflict in teams and apply intervention strategies
- Run effective team meetings
- Facilitate team decision-making
Empower GROWTH
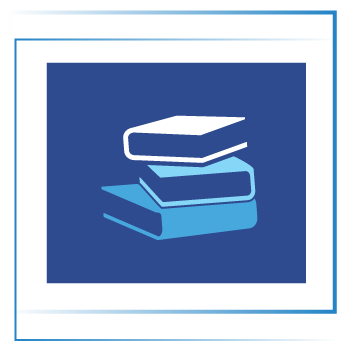
Lean Essentials —5 Days
Purpose
To develop participants as internal experts to successfully lead and execute Lean improvement activities within their organization.
Target Audience
Individuals at any level who will lead and execute Lean improvement efforts to improve efficiency of operations within their organization.
Learning Objectives
- Understand the purpose, objectives, results, and benefits of applying Lean within their organization
- Recognize the five core principles of Lean
- Assess areas of waste within the organization and identify the two key drivers of waste
- Identify, document, and assess Value Streams for improvement opportunities
- Implement Lean tools and methods to tackle waste
- Utilize the A3 framework for problem solving
- Execute Lean improvement efforts using Kaizen/Rapid Improvement Event
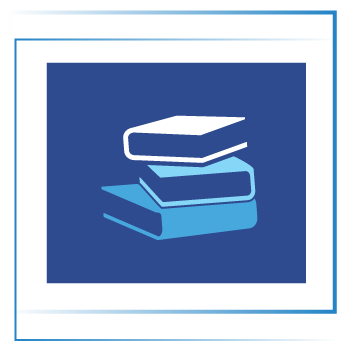
Lean Six Sigma Yellow Belt —3 Days
Purpose
To equip participants with a working knowledge of the Lean Six Sigma improvement methodology, key concepts, and tools used.
Target Audience
Individuals at any level of the organization (front line, supervisor, manager, etc.) who will either participate on a Lean Six Sigma project team, or who will work on small-scale improvement efforts within their own areas.
Learning Objectives
- Understand the purpose and focus of Lean Six Sigma as an improvement methodology
- Communicate with a common language of key Lean Six Sigma terms
- Identify activities in the organization as processes
- Define suppliers, inputs, process steps, outputs, and customers of processes
- Understand and apply the Define-Measure-Analyze-Improve-Control (DMAIC) improvement models to guide process improvement actions
- Apply key DMAIC tools such as project charter, process mapping, basic data analysis techniques, Sigma capability, and root cause analysis
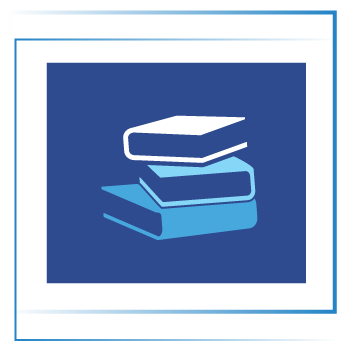
Improve Daily Work —2 Days
Purpose
To develop participants to effectively apply Lean improvements using 5S, standard work, and error-proofing to tackle waste within their work areas.
Target Audience
Individuals at any level who execute improvement efforts to improve efficiency of operations within their work areas.
Learning Objectives
- Understand the purpose, objectives, results, and benefits of applying Lean within their work area
- Recognize the five core principles of Lean
- Assess areas of waste within the work area and identify the two key drivers of waste
- Implement Lean tools including 5S, standard work, and error-proofing to tackle waste
- Understand and apply the A3 framework for problem solving